Filtration & Dewatering Systems
In the pulp and paper industry, filtration is an essential process that separates sediment and other particles from the pulp slurry or wastewater. By removing solid particles, filtration helps to improve the quality of the pulp and paper product. It also minimizes waste in the manufacturing process. There are several different filtration methods available.
Vacuum filtration is a process that uses vacuum pumps to create a pressure differential across a filter medium. This causes the sediment laden water to flow through the filter and leaves the solid particles behind. Vacuum filtration is commonly used in the wire, press, and drying sections of paper machines.
Dewatering is a process of removing water or other fluids from a solid material, such as pulp or paper. This can improve the quality and reduce its moisture content. Dewatering is an essential process that is used to remove excess water from the pulp slurry and paper sheets.
Vacuum dewatering is a process that uses pumps to create a pressure differential across a filter medium or porous roller. This draws out the excess water from the pulp slurry or paper sheet. Dewatering can improve the quality of the pulp and paper product while minimizing waste in the manufacturing process.
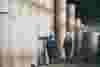